One way to make engines live and have good durability is to have just the right amount of bearing oil clearance. Maintaining a cushion of oil between the bearing and shaft is essential for proper bearing operation and to prevent metal-to-metal contact. Generally, tighter oil clearances are better due to the increased load distribution resulting in less peak loading (see Fig 1). The engine will also run smoother and quieter.
The first question that should be asked is, what is the application, and what is the quality of engine components being used. Race quality rigid connecting rods and crankshafts will allow the clearances to be tighter (.001”-.002”) because there will be less deflection at high RPM’s. Tighter clearances require lower viscosity oils so that the thin oil can enter the clearance space for proper lubrication. Low oil viscosity challenges the bearing and requires materials that can withstand the load under these conditions. Polymer coated bearings (King pMaxKote™) are optimal solution for this since the coating serves as a lubrication layer.
Stock components on the other hand are generally not as precise and rigid as race quality components. The clearances need to be larger (.0025”-.0035”) to compensate for deflections and misalignments. The larger clearances will require a higher viscosity oil to maintain adequate oil film strength. It is better to be a little loose than too tight if you are unsure. Off road and dirt applications need more clearance to allow debris to flow thru the bearings without causing damage.
Crankshaft surface finish also affects oil clearance because a journal surface finish of > 5 RA needs more room to minimize possible metal-to-metal contact. Proper surface finish for racing crankshafts should be < 5 RA. The consequences of both debris in the oil and improper crankshaft surface finish can be mitigated by using engine bearings with a soft upper layer that has good conformability and embeddability properties. King’s polymer coated upper layer can absorb debris and crankshaft surface finish roughness and allow all the parts to continue working in high RPMs.
Nowadays the trend is to use low viscosity oils (0w 10, 5w20) and tight clearances to reduce the drag on the engine resulting in more horsepower and gas mileage. In either case, tight or loose, the oil viscosity must match the clearance so that a proper oil film can be maintained during the life of the engine. Without the proper oil clearance, engines will not survive. One way to achieve desired oil clearances is for the installer to choose a manufacturer that provides engine bearings with consistent wall thickness measurements. King Engine Bearings “Bull’s Eye Tolerance” provides just that in every set. During King’s manufacturing process, bearing wall thickness is constantly computer monitored to ensure that each bearing’s wall thickness fits inside very tight predetermined tolerance limit (see Fig 2). Lastly, all King performance bearing shells go through an automated wall check at final inspection using LVDT technology (see Fig 3). The result is consistent sizing in every set of King Engine Bearings.
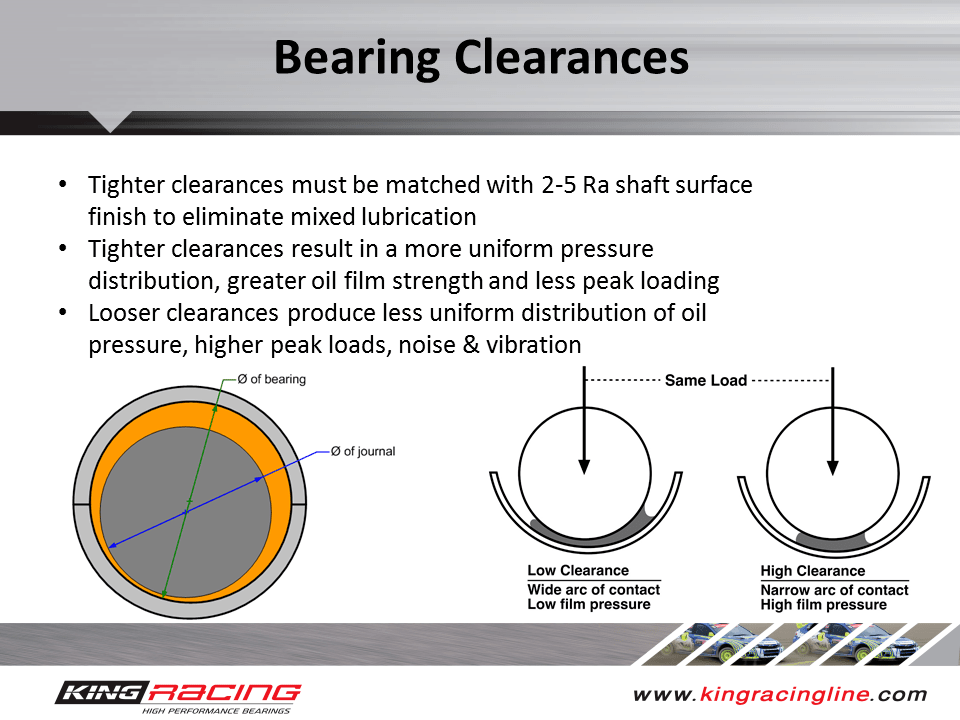


This article was sponsored by King Engine Bearings.
0 Comments